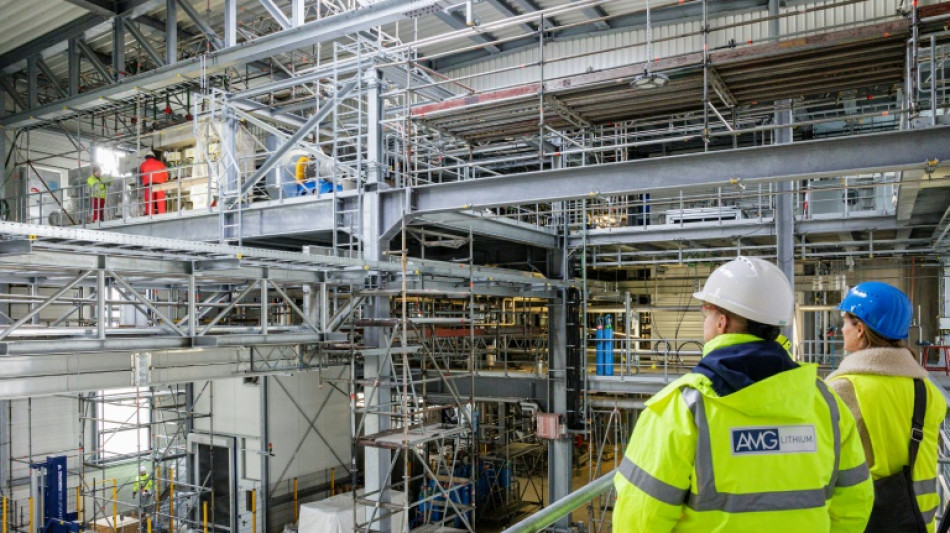
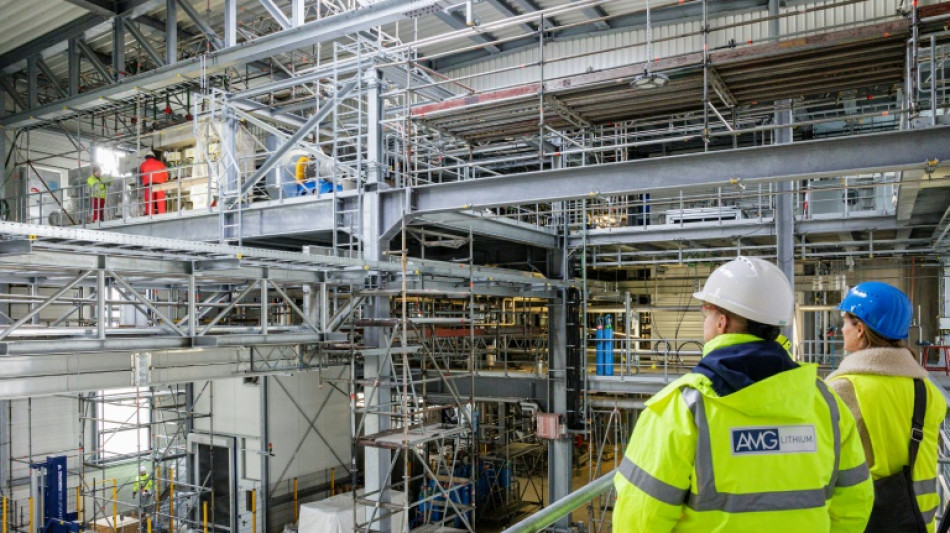
Germany's mine-to-motor lithium supply chain takes shape
Once a byword for environmental disaster due to its heavy industry and mining, the city of Bitterfeld-Wolfen is poised to become a key site for Germany's ambitious green transition.
It is here that the country's first large-scale lithium refinery has been set up, with an aim to play a pivotal role in a European plan to mine and refine its own supplies of raw materials needed to power a fleet of new-generation vehicles.
The white powder the plant will start pumping out from May is a key ingredient in electric car batteries and part of the European Union's recipe to reduce its dependency on foreign imports.
The take-off in demand for batteries was "foreseeable", said AMG’s CEO Stefan Scherer, and his company has been "able to ride the wave".
Bitterfeld-Wolfen in eastern Germany had been picked to house the new factory because of its "proximity to clients", Scherer said.
The plant's installation closer to battery makers could counter supply risks for Europe, whose reliance on imports has come to be seen as a liability amid rising geopolitical tensions –- most notably with China.
The Asian giant is not the biggest producer of raw lithium, but possesses a majority of the world's processing capacity, as well as a big chunk of battery production.
The exposure to potentially unreliable suppliers -- and a desire to have a larger share of the industry -- is behind EU plans unveiled last year to increase domestic extraction and processing of lithium and 33 other "critical" materials.
"We are already in talks with politicians to discuss the financial resources for future expansion," said Scherer, whose factory is at the centre of the new network.
- Production potential -
The first module at AMG's plant will be able to produce 20,000 tonnes of lithium hydroxide annually -- enough for around half a million car batteries, depending on the size, said Scherer.
More units could be added over time to increase production fivefold to 100,000 tonnes, enough to cover "up to 20 percent" of the demand in Europe, he speculated.
The EU plan to secure supplies aims to do 40 percent of its processing for the designated critical materials domestically by 2030.
For German industry -- and particularly automakers -- bringing lithium production closer to home "increases their resilience in case of international supply chain tension", said Yoann Gimbert, e-mobility analyst at the Transport and Environment think tank.
Companies that need to exchange raw material supplies quickly to get a product that meets their standards could be a case in point.
"Instead of having to laboriously ship these containers back to Asia via Hamburg, you can bring them a few 100 kilometres here to Bitterfeld either by truck or ideally by train and we can exchange them practically within a few days," Scherer said.
While the AMG's project will initially be supplied with lithium from the company's mine in Brazil, the raw product could eventually come from closer to home.
Close to Germany’s border with France, the Australia-based group Vulcan Energy began a pilot scheme at the end of last year to filter lithium from subterranean waters.
- Mine project -
Closer to Bitterfeld-Wolfen, Zinnwald, a small village near the Czech border, an AMG-backed project is taking the more conventional approach to mine lithium ores from the ground.
Sourcing larger amounts of lithium locally will prove to be more of a challenge -- a fact reflected in the European Union's more modest 10-percent target for extraction.
But projects like the one in Zinnwald could still be a "vital cog", Zinnwald Lithium's CEO Anton du Plessis told AFP.
To anchor green industries in the EU, "it needs to ensure that it has the overall supply chain", including extraction, said du Plessis, who hopes to see the Zinnwald mine in full operation by the end of the decade.
While extraction would only be a partial solution, new planned processing capacity in Europe could "fully cover demand", said Cornelius Baehr, an analyst at IW Consult.
Whether all those projects will be realised remains uncertain, Baehr said, and the lead-in times for new production sites -- somewhere between five and 10 years -- meant the EU's 2030 target "will not be easy to reach".
M.Fierro--IM